Building Success Series Features the Carpenters' Joint Apprenticeship Training Center
This quarter, the Building Success Series found itself speaking with Michael Papalia, Training Coordinator and State Director of the United Brotherhood of Carpenters’ Joint Apprenticeship Training Center (JATC or ‘the Center’) of Ohio. The conversation revolved around one of the surest ways to position oneself for future success: Education.
There are five key elements involved in a thriving educational institution. The JATC has combined those elements to bring about a training center for union carpenters and millwrights that is considered among the construction industry as being the best in the United States. Those elements include the facility, faculty, student body, community, and leadership.
The 60,000 square foot JATC campus sits on 12 acres of wholly-owned property in Richfield, Ohio. More than 500 apprentices and 700 journeymen are trained at the Center each year in specialized shops for carpentry, floor covering, millwrights, pile drivers, residential structures, interior systems, and more. Its state-of-the-art technology center offers computer training to apprentices as well as journeymen. Apprentices can earn an Associate of Applied Science Degree in Applied Industrial Technology from Cuyahoga Community College (Tri-C). Each year, more than a half-million hours of apprenticeship training and 13,000 hours in journeyman upgrade training are completed. To date, the Center has helped place more than 2,200 professional union carpenters in the field over the last 15 years.
The Center offers several advantages over a traditional four-year college. First, there is no tuition cost for the students. Throughout the four years of training, the only school-related cost is for books, which is around $400. Second, as an apprentice, the student receives pension, annuity, and health & wellness benefits. Third, after finishing the program, they will have one-plus year’s credit to an associates’ degree per an agreement with several universities, should the student wish to continue their studies in safety, construction management, or other related fields.
Finally, there is the pay. Apprentices start out at $14 an hour and get increases every six months that they are in the program. If a student starts his or her apprenticeship straight out of high school, by the time they finish in four years, they have the potential to be earning $60,000 a year as a journeyman carpenter with no college loans to pay back. If they keep at it and are able to prove themselves, they can achieve promotions to foreman or superintendent, and earn more than $150,000 a year. Eventually, they may even start their own company where the sky is the limit.
There are also the benefits of making a good honest living. Mike talked about growing up in Pittsburgh: “Driving around downtown with my father, he would always say, ‘I built this building,’ or ‘I worked on that bridge.’ As a kid, you knew he was going to say it every time we drove by, and I would say to him, ‘Dad, how many times are you going to tell me that?’ The thing is, with my kids, I did the same. There is a great pride in the work that we do. Pride helps bring about success. You don’t have to be the best. If you can be reliable and dependable, you can be a successful person in our trade.”
It comes as a surprise to some that the median age for apprentices is 27 years old. “We really get all types of people as our students. Some are right out of high school. They are part of a family tradition in the construction industry. They excelled at their high school’s Vo-Tech programs, and they want to make their family proud,” Papalia said.
Our best apprentices are usually in their mid-twenties. They have a bit more maturity and are ready to work. Having more experience in the real world lets them appreciate the learning opportunities we make available to them. Then again, we’ve had guys in their 40s who have been down on their luck for the past 18 years, and they’re looking to make a change. With a little guidance they can be great as well. No matter what their background, our job at the JATC is to take these students, build them up, and put them in a position to succeed.”
One of the ways Papalia said the Center’s staff accomplishes this is by running the program like a job site. “If a student is five minutes late, we send them home. There is zero tolerance for lateness. We also have zero tolerance for absenteeism. Our apprentices know it and our contractors appreciate that. In fact, we have signs all over the center that say, ‘Absenteeism is the number 1 cause for termination.’ The students don’t like it, but it’s the truth. They are not going to be handed any breaks out in the world, so they don’t receive any here.”
Papalia goes on to talk about the quality of the students that the Center produces. “Nowadays everyone is concerned with the bottom line, which they should be. However, looking for the low bid isn’t always the best way to go. The low bid is often unqualified, unskilled labor. In the short term a customer may save a little bit of money. Unfortunately, the recall [of a team] to come back out is often times more expensive than having it done right the first time. The cost of cheap installation comes back to haunt a customer down the road. That is why I always preach the 5 P’s: Proper- Preparation-Prevents-Poor-Performance. When a student makes it through the Center, you know they are going to be able to do a job right, the first time.”
When asked why the JATC stands out over other programs, Papalia immediately talks about the training. “Our training is really what separates us from the non-union. We’ve been training apprentices for over 130 years, but we also have the most current technology, the most current tools, and we train for production AND safety. We want to make sure that all of our workers go home at the end of the day with ten fingers, ten toes and not all banged up.”
The Center’s nine full-time instructors have a combined 250 years of experience. Papalia emphasizes that his instructors are not only masters of their trade, but are also master communicators.
In order for an instructor to work here, they have to be recommended as an industry expert. We’ll talk, have a formal interview, and if we feel they have the ability, we’ll bring them in to teach part time. Every one of our instructors could be a superintendent in the field. They are well-rounded at their craft. Just because someone is good with tools, doesn’t necessarily mean they will be good with students. They must be able to prepare lesson plans. They need to understand if their students are learning the material. If students are struggling, the teachers have to make material accessible. Additionally, our instructors have to connect with the mindset of students. They can’t just say, ‘This is how we did it back in my day.’ Kids are too smart for that. There is too much information available out there to believe otherwise.”
Along with high schools and Vo-Tech programs, the JATC receives tremendous support from local chapters of the United Brotherhood of Carpenters, the Association of General Contractors and the Indiana/Kentucky/Ohio Regional Council of Carpenters. The JATC’s advisory board reads like a Who’s Who in the NE Ohio construction community, each adding their experience and expertise as they help facilitate the next generation of carpenters, superintendents, business owners, and leaders.
One cannot properly describe the Joint Apprenticeship Training Center without mentioning its director. The son of a carpenter, Mike Papalia, graduated from his own apprentice program in 1982. He spent the next fourteen years working with his tools before being offered an opportunity as a Health and Safety Expert for the UBC in Washington, D.C. he travelled 40 weeks a year from coast-to-coast, teaching health and safety in the early 90s. Afterwards, Mike worked as a lobbyist with the UBC for 8 years on Capitol Hill.
“At one meeting there were 18 other people, Vice President Al Gore, and me. I kept thinking that if my friends could see me now, they’d never believe it. Here I am, a knucklehead carpenter, meeting with the Vice President of the United States. Don’t get me wrong, when I say ‘knucklehead carpenter,’ I say it with pride; but, the whole time I’m waiting for people to catch on and realize that I’m not supposed to be there.”
In February of 2003 Mike took over as the Training Coordinator of the JATC. His attention to detail and high standards for which he holds both students and faculty are evident from the first moment one steps inside the Center. Each work area is kept in pristine condition. Tools are picked up, floors are swept, and modules are in a constant state of readiness. The pride he takes in his facility, his work, and his profession set the ultimate example for all those who progress through their own apprenticeship.
Grateful for everything the carpenters union has done for both him and his family, Mike holds firm to the belief that every man or woman who works hard has the right to a pension, healthcare, a safe work environment, and deserves to have those rights negotiated for them. While not everyone is able to stand on the top rung of the ladder, they should have the opportunity to be successful in their own right.
Despite his modest refusal to admit it, Mike did belong in the same room as Vice President Gore. In all he does, there is poise, pride, and performance. His education, which can be traced back from master to apprentice from more than 130 years, has enabled him to become an expert craftsman, communicator, negotiator, educator, and a leader. Moreover, it has helped hundreds of others find the path to their own success.
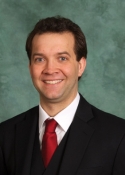
Blake J. Minich is Marketing Director at Applied Financial Concepts, Inc.Financial Advisors to the Construction Industry since 1971.